Case Study: Manufacturer Of Keys & Locksets
Company Background:
The company designs and manufactures keys and, mechanical and electronic locksets for the automotive industry. They have global operations with over 5,000 employees in eleven countries. The company aggressively pursues manufacturing innovation through the use of flexible manufacturing technologies and automation.
Challenge:
Management wanted to automate elements of their insert molding process. The automation targeted bulk handling, sorting, heating, and placement of 5 different styles of inserts into a plastic injection mold machine with load tolerances between .0005” to .002”. The customer also wanted to automate the process of removing finished parts, part verification for sorting, checking of magnetic field strength, and removal and disposition of the runner.
Assessment:
The current process required an operator to manually load and unload inserts, inspect magnetic field strength, and verify the part. Clearances in the mold made the load process difficult, increasing part-to-part cycle times and scrap. Acieta determined that automating the process would require two robots, one dedicated to bulk handling and staging, with the other managing the handoff between staging and the molding machine.
Solution:
The solution required the coordinated actions of the two FANUC robots, an LR Mate 200iB and M-6iB/6S. The LR Mate removed processed inserts from an Acieta designed recirculation conveyor system. A FANUC VisTRACi vision system sorted individual inserts based on characteristics for robot staging. The LR Mate also serviced an Acieta designed magnetic dispenser system. The M-6iB/6S robot would select the sorted and staged inserts, and could heat inserts prior to placing them into the mold. The robot would remove finished parts, place inserts into location and discharge completed parts.
End Result:
Consistent part load/unload cycle time and quality, improved overall part-to-part cycle times and forecasting. Preheating inserts further improved quality by reducing the temperature differential between the insert and the injected plastic. Automation provided cost advantages by eliminating the manual processes of magnetic field inspection, part sorting, and verification. An operator tends the system only to add parts to the hopper and occasionally inspect parts.
To discuss known AUTOMATION OPPORTUNITIES or discover new ones:
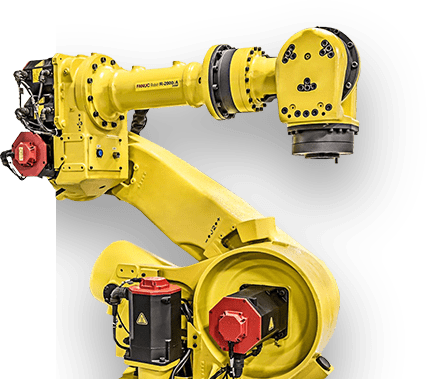