High temperatures, molten metal, dust, noise and fumes can make foundries unpleasant and hazardous places for people, but ideal locations for robots. Foundry robots can perform many of the most dangerous or repetitive tasks within these environments. They can automate certain jobs to remove the risks to human workers and improve efficiency. Acieta is an experienced integrator who can help your business realize the many benefits foundry automation equipment can bring to your operations.
Foundry Automation
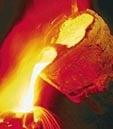
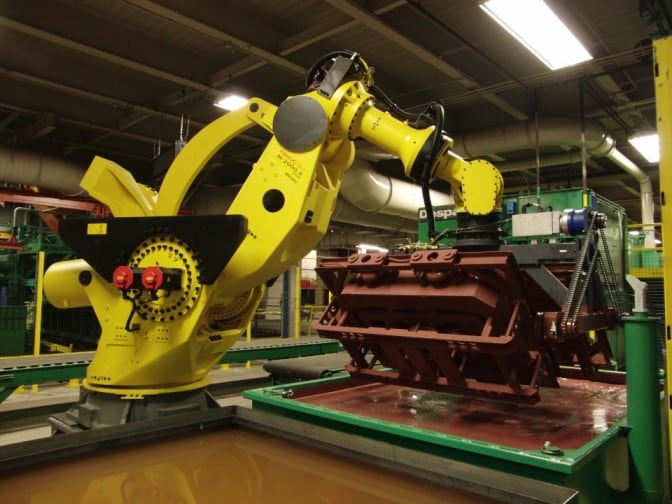
Sand casting foundries offer many tasks for robots. Robots for handling sand castings reduce damage. Robots for metal skimming, pouring and core assembly produce less scrap with far less temperature variation.
Tending die cast machinery, ladling molten metal, spraying mold release and trimming excess metal are all excellent applications for foundry robots. Producing quality castings demands consistent process timing, a great benefit of deploying advanced foundry automation equipment. Robotic die casting produces consistently high-quality results thanks to its precision controls. This means there are far fewer errors that come off the production line, which leads to higher customer satisfaction and significant cost savings in the long run.
In addition, these systems also help keep workers safe by taking potentially dangerous jobs off their shoulders. Because these robots can perform such tasks without fear of harm, operators can avoid losing time to injury and feel more satisfied with their jobs.
Foundry and Die Robotics Applications
The Acieta team has implemented many foundry automation systems and understands the special requirements of this challenging environment. Here are some of the best-suited application areas:
- MATERIAL HANDLING – Pouring molten metal takes a steady hand, and nothing is more stable than a robot. Optimized to deliver the same quantity every time, a die casting automation robot skims dross and ladles metal more steadily than any human, which eliminates turbulence and spills. The same goes for loading inserts and extracting solidified castings, where the die is cooling while open. Die casting robots can reach between dies too hot for a human — saving energy and reducing cycle time.
- MATERIAL REMOVAL – Sprue: the unwanted runners, risers and flash — is inevitable in casting and must be removed before pieces move to downstream operations. Foundry robots can carry grinding wheels or other cutters to trim away this unwanted material, or could load cast shapes into a de-gating or trimming press. In a high-volume cell, one robot could unload and place the pieces while the second wields the cutter, or when volumes are lower, a single robot might do both jobs — changing tools, as needed.
- SPRAYING – Dies often need a film of lubricant spraying over their surfaces while open. Access is poor, mist obscures the view and fatigue quickly occurs. This leads to excess lubricant in some areas and insufficient lubricant in others. The result is uneven die cooling and casting defects. For die casting robots, it’s a straightforward task. They just follow the programmed path every time.
- FOUNDRY OPERATIONS – Sand casting foundries are a little different yet have many similar tasks for robotic foundry automation. Handling sand castings is one example where damage is reduced. Metal skimming and pouring, core assembly and extraction are others.
Whether you’re in foundry and die or another industry, Acieta’s robotic automation solutions can help your business, identify opportunities and support you through every step of your project. Get started by contacting us today.
To discuss known AUTOMATION OPPORTUNITIES or discover new ones:
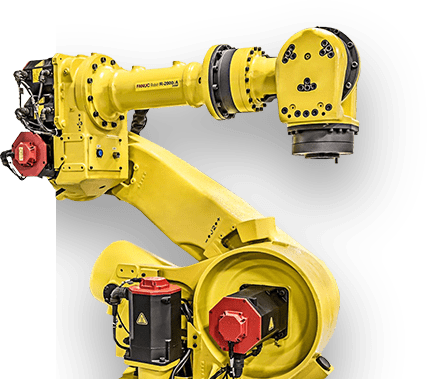