New developments in robotics are helping agriculture companies be more competitive by increasing productivity and reducing operating costs. Producers, growers, and equipment OEMs are using robotic technology to quickly handle the more time-consuming tasks.
Agriculture
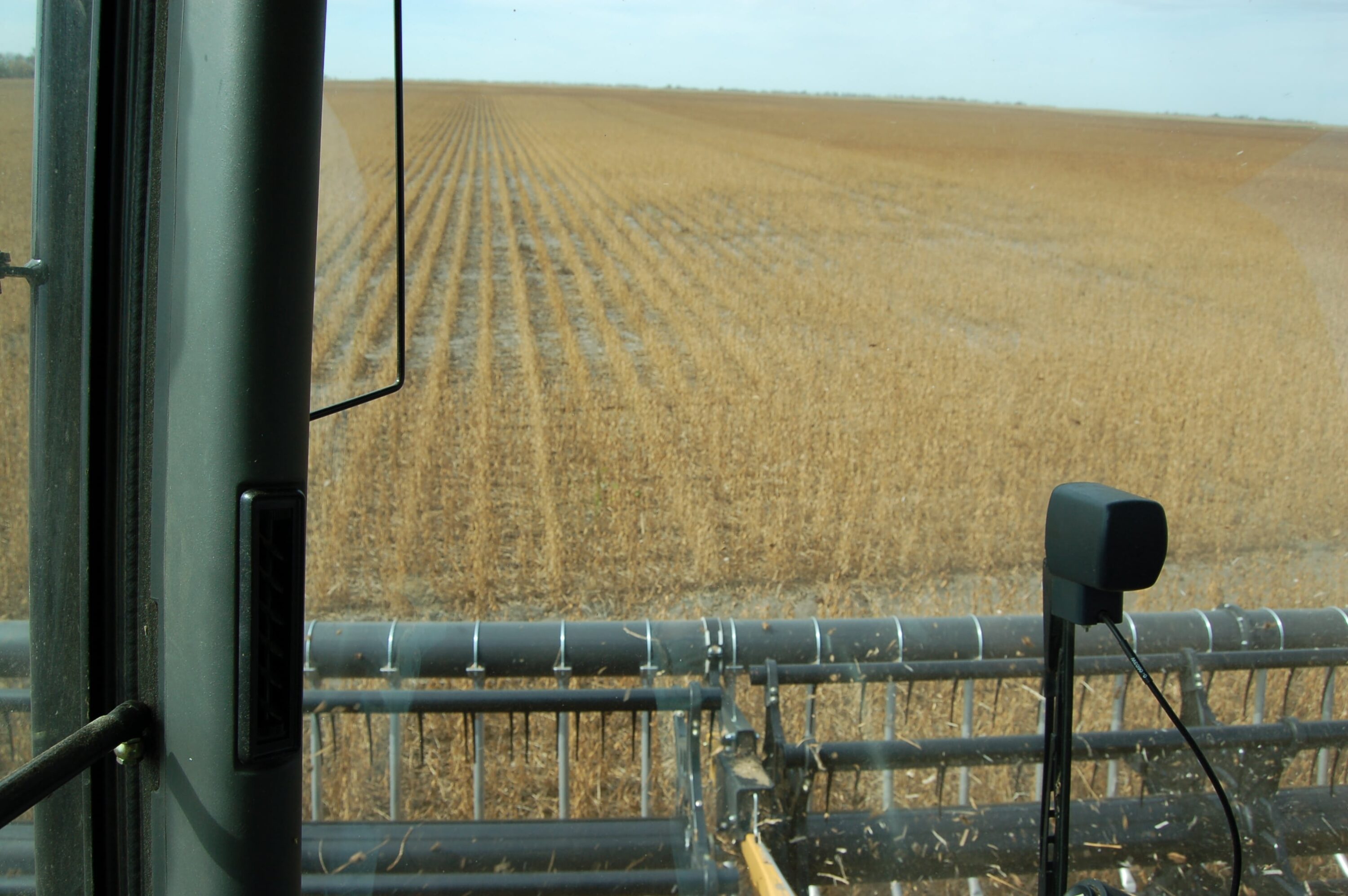
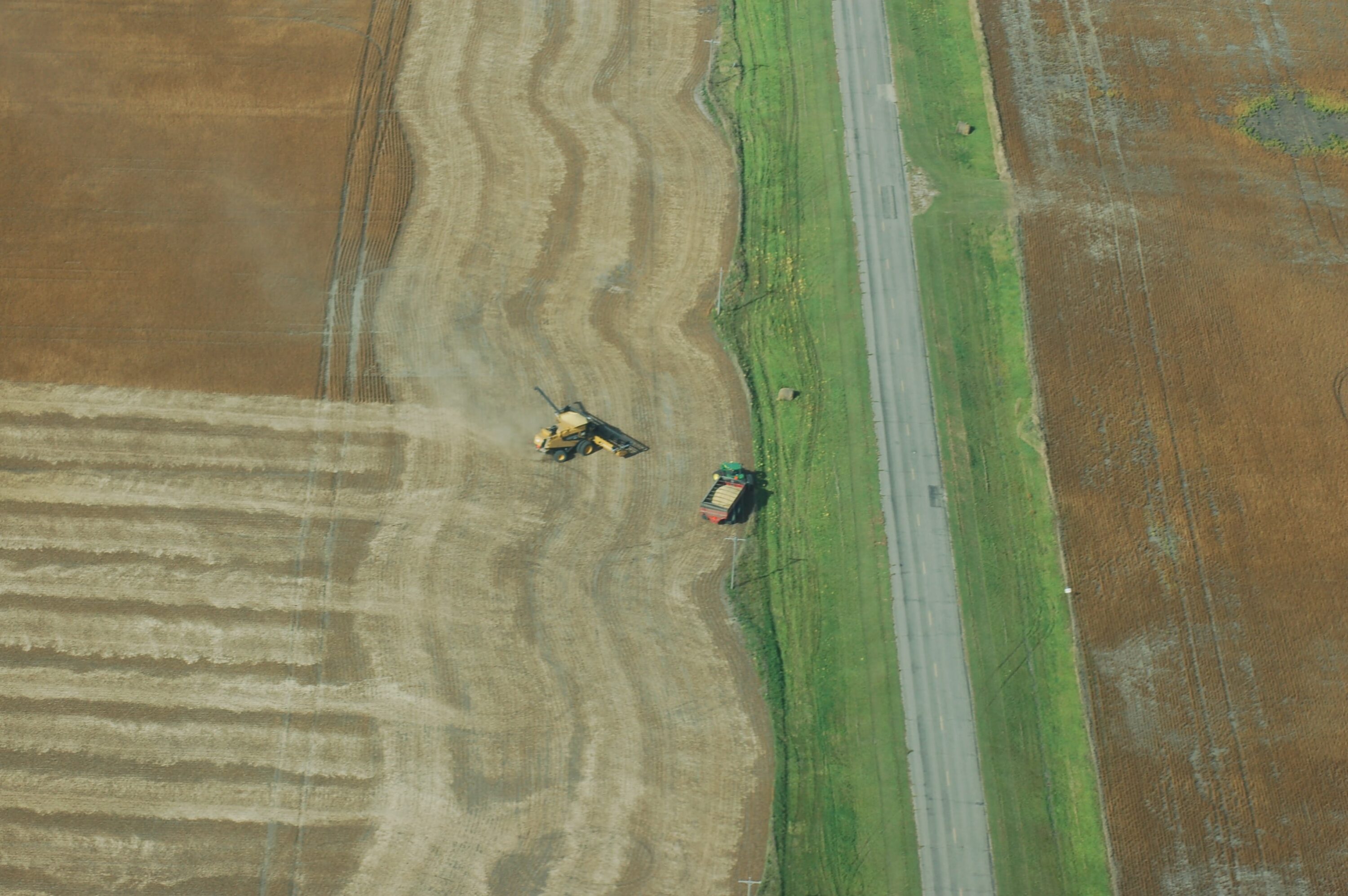
Labor shortages challenge most agriculture companies, especially those with working environments that are repetitive, dirty or dangerous. Using robots to supplement the existing workforce lets a business accept more orders without being limited by worker availability. It’s hard to keep laborers in fatiguing jobs that require constant heavy lifting. Reassigning an operator from a repetitive, unskilled task to a more challenging, skilled job improves throughput and process efficiency.
Safety improvements often outweigh any robot investment costs. Repeated lifting and twisting cause injuries that lead to time away from work. In jobs like these, a robot creates a much safer working environment.
Workers in engaging and rewarding jobs are more likely to stay and take an interest in the success of the team. Reducing employee turnover and eliminating the need for repeated training of new employees saves time and keeps production running smoothly without interruption, which translates to profitability.
Agriculture Robotics Applications
As agriculture companies continue to use robots, there will be more opportunities for them to become even more competitive. Greater capacity, higher quality and less reliance on labor will lead to higher profits.
Ag equipment manufacturing (machines for planting, monitoring, harvesting and picking)
As farm equipment continues to incorporate more advanced technological features, the challenge is to avoid significantly increasing price beyond what the customer will pay. To stay competitive, farm equipment must stand out against others in the industry and provide real advantages to farmers, with such features as mapping programs, monitors and rate controllers.
Today, OEMs use robots for the more repetitive, dull or dangerous jobs, such as welding, machine tending, inspection, and heavy part lifting. By switching part fabrication to a robotic system, many OEMs increase productivity an average of 50 percent, reducing scrap, and recovering a return on investment in 12 to 18 months.
Research and Testing
In the development of a new product, there may be needs for large-scale testing and research, which can include testing samples and batches repeatedly every day for long periods of time. Robots can collect and store data electronically quickly for analysis later. Robots are consistent and reliable, so research has the highest level of accurate information.
Inspection
Inspecting and sorting products on a conveyor is mind-numbing work that’s subject to human error. Using advanced cameras and visions systems, robots can continually and consistently sort products of different sizes and shapes or identify and eliminate bad products from the product stream to ensure optimal quality.
Packing and Shipping
A robotic arm can be outfitted with custom tooling to handle crops of all sizes and shapes—even delicate fruits and vegetables. Produce can be sorted and packed in cartons or bags, then palletized and shrink wrapped without any human contact.
To discuss known AUTOMATION OPPORTUNITIES or discover new ones:
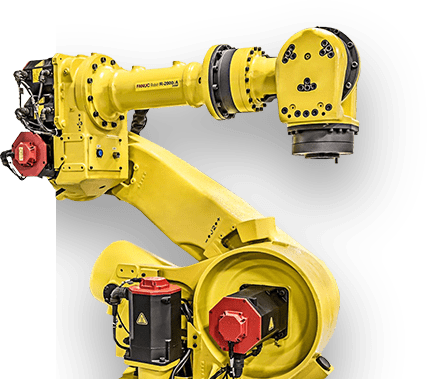