Staying competitive in today’s landscape demands strategic investment in scalable, intelligent automation. Robotic systems are no longer limited to isolated, repetitive tasks. When integrated properly, they can enhance throughput, improve quality, and solve persistent labor and efficiency bottlenecks across the value chain.
General Manufacturing Automation
Industrial Automation Solutions
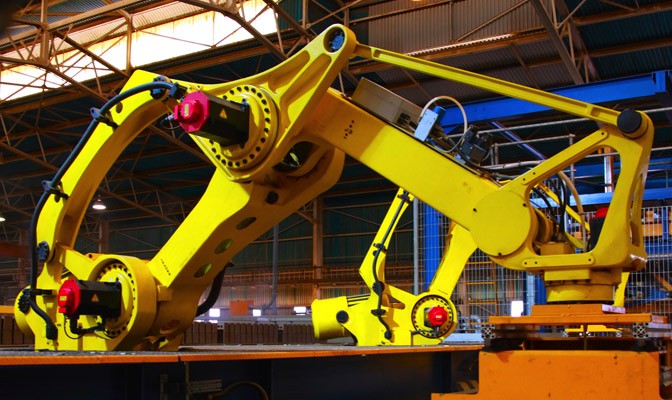
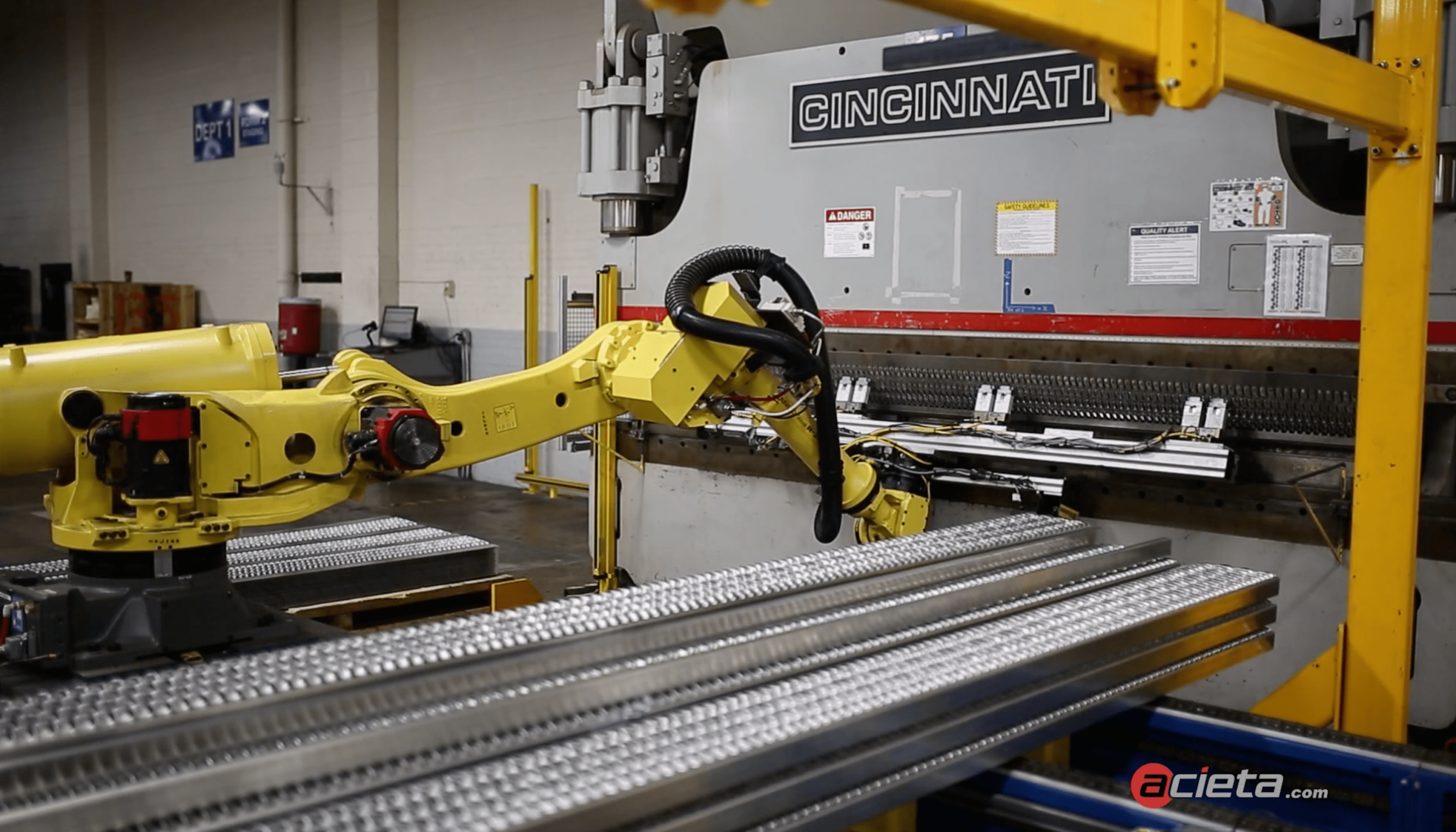
Industrial Automation Solutions
We see the strongest success stories when automation is deployed to solve high-impact operational problems. Common scenarios include:
- Assembly: Robotic systems support precise component placement, fastening, press-fitting, and sealant application, improving consistency and cycle times in complex assemblies. When combined with vision and force control, robots can manage part variability and tighter tolerances in multi-stage processes.
- AMR Integration: Autonomous Mobile Robots (AMRs) enhance intralogistics by dynamically transporting materials, parts, and finished goods between work cells, storage, and shipping areas. When integrated with robotic workstations, AMRs reduce manual transport labor, improve line-side delivery accuracy, and enable true end-to-end automation across the facility.
- Machine Tending: Robots reliably load and unload CNC machines, injection molders, press brakes, and other production equipment, reducing idle time and increasing spindle utilization. With capabilities like part orientation, in-process cleaning, and automated inspection between cycles, machine tending robots help maximize equipment ROI while minimizing operator intervention and downtime.
Material Handling: Robots equipped with advanced grippers and vision systems reduce damage and cycle time in part transfer, kitting, and bin-picking operations.
Material Removal: Robots deliver uniform finishes in grinding, deburring, or sanding operations, which are typically high-risk and ergonomically challenging for humans.
Metrology & Inspection: Integrated measurement systems paired with robotic arms automate part verification with sub-micron accuracy, enabling in-line quality checks and reducing dependence on manual inspection stations. This ensures higher throughput without compromising compliance or traceability.
- Welding & Fabrication: High-accuracy weld paths and consistent heat input improve structural integrity and minimize rework, especially in high-strength alloys.
Addressing Labor and Productivity Gaps with Automation
The current labor market, especially in skilled trades and repetitive task areas, continues to present challenges for manufacturers. Robots offer a long-term solution — not by replacing skilled workers, but by reallocating human talent toward higher-value tasks.
Fully Autonomous Systems: Ideal for repeatable, high-volume workflows where uptime and part consistency are critical.
Collaborative Robots (Cobots): Suited for hybrid work cells, enabling safe interaction between humans and robots on shared tasks without the need for extensive guarding or redesign.
Benefits Beyond the Basics
While uptime, cycle time, and error rates are common metrics, the real ROI of automation often lies in how systems enable broader operational goals:
Throughput Consistency: Robots maintain takt time under any shift condition, reducing production variability and downstream disruption.
Workforce Stabilization: Automation fills key gaps without increasing hiring pressure, supporting lean teams and extending operational scalability.
Quality Assurance: Robotic precision supports tighter tolerances and reduces human error in inspection, handling, and assembly tasks.
Safety Outcomes: By offloading tasks with high ergonomic risk or exposure to hazardous materials, manufacturers reduce injury rates and related costs.
To discuss known AUTOMATION OPPORTUNITIES or discover new ones:
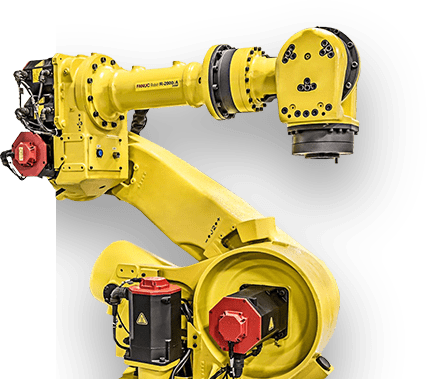